RDG Series Sulphur Drum Granulator
Product Description
Working principles:
There is melted liquid materials and cooling water pipeline, and numerous atomized shower nozzle on the pipeline inside rotary cylinder with many lifting plates. With the revolution of the cylinder, the lifting plates constantly bring powders or granules in the lower side of the cylinder to the upper side of the cylinder, and down to the lower side of the cylinder, forming continuous material curtain; on the other side of material curtain, liquid materials and cooling water spray from their own shower nozzle to the material curtain inside the cylinder respectively. The liquid atomized materials contact with fine granules, and spray themselves on them, and make fine granules form increasingly bigger spherical particles; atomized cooling water makes granulates sprayed with liquid materials quickly cool and solidify. As the revolving cylinder tilts down along discharge end in axial direction, liquid materials experience three stages inside the cylinder, namely, generation, size increase, and forming of seed crystal (powder or fine granules); spherical particle products satisfying particle size requirements are obtained at the discharge port. Cooling water sprayed is transformed into water vapor with the sensible heat and latent heat of solidification, and drains with the off-gas by draught fan after undergoing dedusting.
Particle size and particle size distribution of solidified materials can be adjusted by adjusting flow rate of materials and cooling water, and speed and angle of inclination of the cylinder, and particle size generally ranges between 2 to 10 mm. In the meantime, flow rate of liquid materials and cooling water is real-time controlled by computer by detecting temperature at different points inside the granulator, making the materials quickly cool, and effectively preventing excessive water content in materials.
Scope of application:
It is applicable to melted materials that are hydrophilic and insoluble in water, and require condensation and solidification, and granulation, with a low liquid viscosity, high melting pint or softening point by principle. Typical applied materials: sulphur as an example.
Performance characteristics:
● Melted materials directly contact with cooling water, featuring high cooling efficiency, quick solidification, and high productivity of single machine. In terms of sulphur, the maximum productivity of single machine reaches over 22T/h, which is equivalent to the productivity of three to four rotary steel belt granulators.
● Atomized cooling water directly contacts the surface of particle materials; Latent heat vaporized by cooling water takes away the heat of materials, making materials quickly solidify and shape, with less water consumption and without circulating water treatment.
● As particle is layer-by-layer sprayed from small size to big size and layer-by-layer cooled and solidified, and the finished particles are compact. Compared with underwater granulation, there is no air hole inside the particle, and the particle has a low water content which reaches as low as 0.4. The water content under underwater granulation reaches 2%. Compared with rotary steel belt granulation, its finished particle features big bulk density, low fragility, and good flowability. Its bulk density can reach 1.15 to 1.3. Bulk density by rotary steel belt granulation can reach 1.0 to 1.1, with flat and fragile particles.
● Flow rate of liquid materials or cooling water is real-time controlled by computer by detecting temperature at different points inside the granulator, making the materials quickly cool, and effectively preventing excessive water content in materials.
● Particle size and particle size distribution trend of finished particles can be adjusted by adjusting flow rate of materials and cooling water, and speed and angle of inclination of the cylinder, and particle size generally ranges between 2 to 10 mm.
● Besides, it also features small floor space, less investment, lower energy consumption, less maintenance, and continuous and stable system.
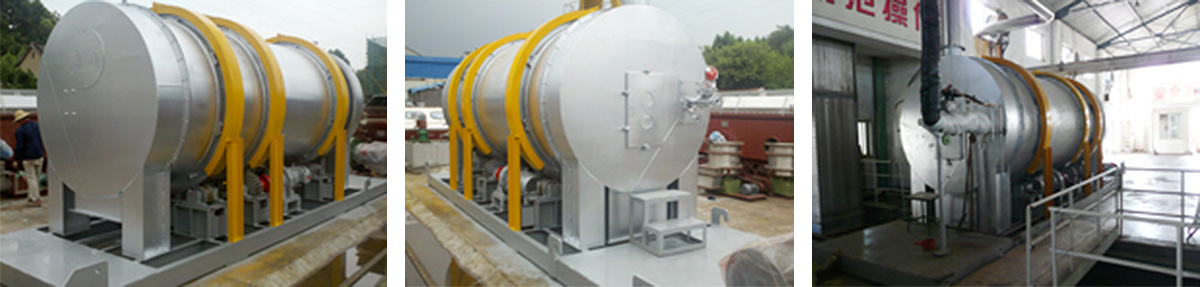
Specification and model:
For sulfur granulation, its single unit production capacity has formed various specifications such as 8T/h, 15T/t, 25T/h.
Other material systems, depending on physical properties.
Online inquiry